In today's fast changing consumer market, manufacturers, brands and retailers must meet product quality and safety requirements. Consumers now look for transparency in the products they buy. With the ever more diversified supply chain, brands and retailers face more challenges in ensuring product quality and compliance.
At QIMA, we understand the challenges you are facing. Our team of trained experts and ISO 17025 accredited labs in Asia, Europe and the Americas help you to achieve product compliance in various consumer products including softlines, hardlines, electrical & electronics, and toys & juvenile products.
Through our online digital platform, you can access real-time results on how your products and suppliers are performing.
From engineering products to analysing test results, our experts make sure you are getting the support you need in regulatory knowledge, designing testing protocols, receiving accurate test data, and providing analytics that will help you ensure product compliance with continuous improvement on product quality.
Testing Capabilities for Your Product and Industry
Our state-of-the-art laboratories offer testing for a number of product categories, including softlines, hardlines, electrical & electronics, toys & juvenile products and more.
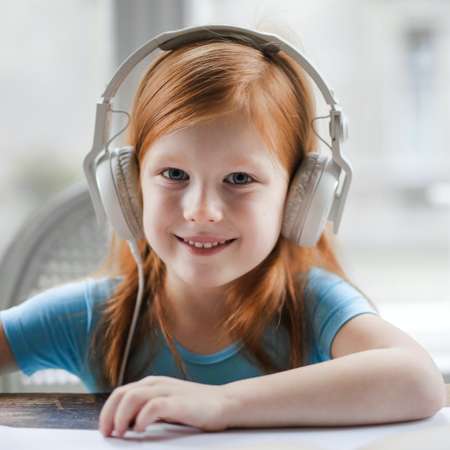
Electrical & Electronics
QIMA offers lab testing services for a wide range of electrical and electronics products.
Need more information?
By contacting QIMA you agree to our privacy policy and terms and conditions.
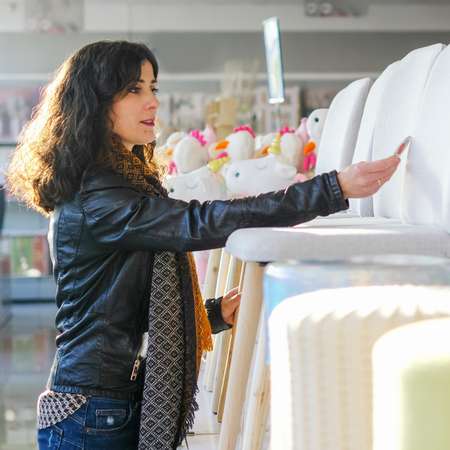
Hardlines
QIMA’s hardlines expertise ranges from eyewear, food contact materials, furniture, sporting equipment and more.
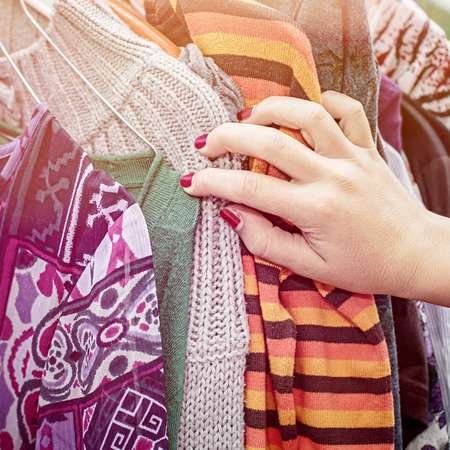
Softlines
QIMA has dedicated expertise specifically for the garment & apparel, footwear and fabric industries.
Bags & accessories
Reusable fabric masks
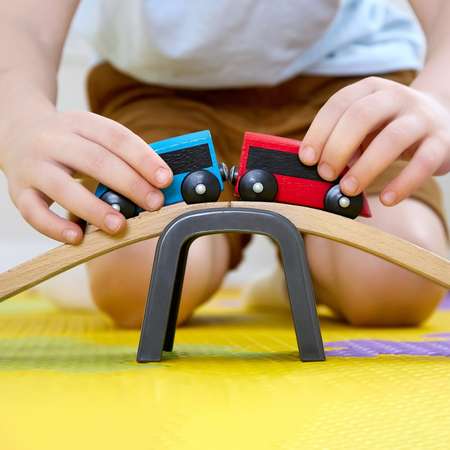
Toys & Juvenile Products
QIMA offers lab testing services for every category of toys and juvenile products against a number of international standards (including EN, ISO, ASTM, IEC).
Take a Tour of Our Labs
Get a full view of QIMA's laboratories, where we address the product safety compliance needs for clients in 120 countries.